Silicone molding and Vacuum Casting
You are here » Home »
Silicone molding, vacuum casting, duplication
As you have read on the 3D Printing page, there are 3 main categories of 3D printing technologies: FDM, SLA, SLS.
But 3D printing is not only about these 3 technologies.
Here we will talk about silicone molding, vacuum casting and duplication.
Vacuum casting is a duplication technique used for the production of small series of highly functional plastic parts. The materials used for vacuum casting are two-component polyurethanes which are cast in a silicone mold to obtain high quality parts.
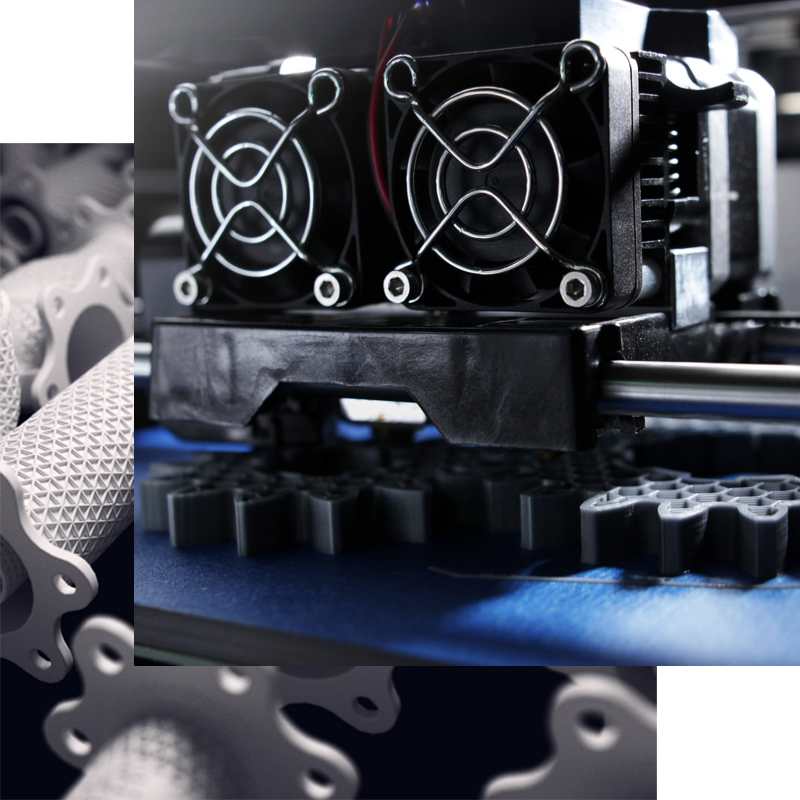
1 – 3D printing of the part
Vacuum casting is a rapid prototyping technology for which it is necessary to have a basic model. To obtain this model, we use additive 3D printing technology.
Generally, we use stereolithography (SLA) for its high precision and quality of detail.
2 – Making the silicone molding
From the part obtained in 3D printing, we cast silicone around the model (under vacuum, to avoid air bubbles). Once the silicone hardens, we remove the 3D printed part by cutting the mold according to the parting line, which leaves a cavity that will allow us to cast the material in order to obtain a duplication of the original part.
3 – Vacuum casting and duplication
Once the mold is obtained, all that remains is to pour the resin inside (via the cavity obtained in step 2). We use a vacuum casting machine to eliminate air bubbles. Then the resin is cured by baking it. Finally, the mold is opened and the finished part is obtained.
This part is the exact copy of the part obtained by 3D printing and which was used to manufacture the silicone mold.
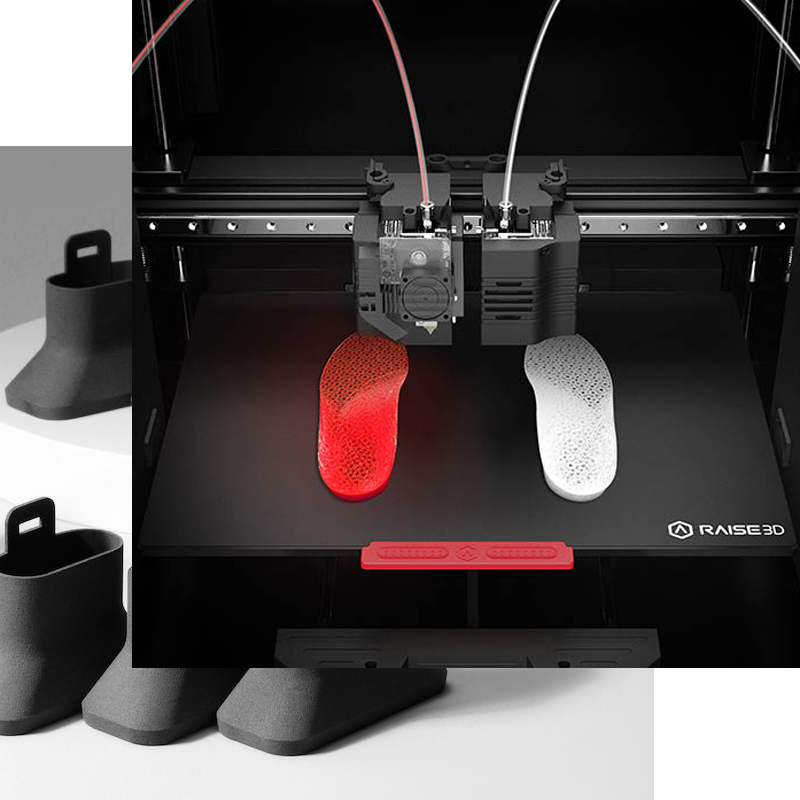
Why choose silicone mold and vacuum casting?
Duplication by silicone mold and vacuum casting allows to obtain parts of a superior quality, comparable to injected parts, but at a much more accessible cost (keep in mind that a metal mold for injection can cost several tens of thousands of dollars while a silicone mold costs a few thousand dollars).
The models obtained by vacuum casting are therefore particularly suitable for functional testing and final validation testing, for marketing purposes and for the production of final parts in limited quantities (a silicone mold allows us to produce between 15 and 20 parts before deteriorating).
Moreover, we can obtain different levels of finish (smooth, matte, glossy, satin, rigid, semi-rigid, elastomeric, opaque, transparent).
Since this process is complex, it is essential to carry out a feasibility study before starting the project. This is why it is not possible to obtain an estimate online as for FDM and SLA 3D printing.
To get an estimate, contact us via our contact page.
Example of duplicated parts in vacuum casting
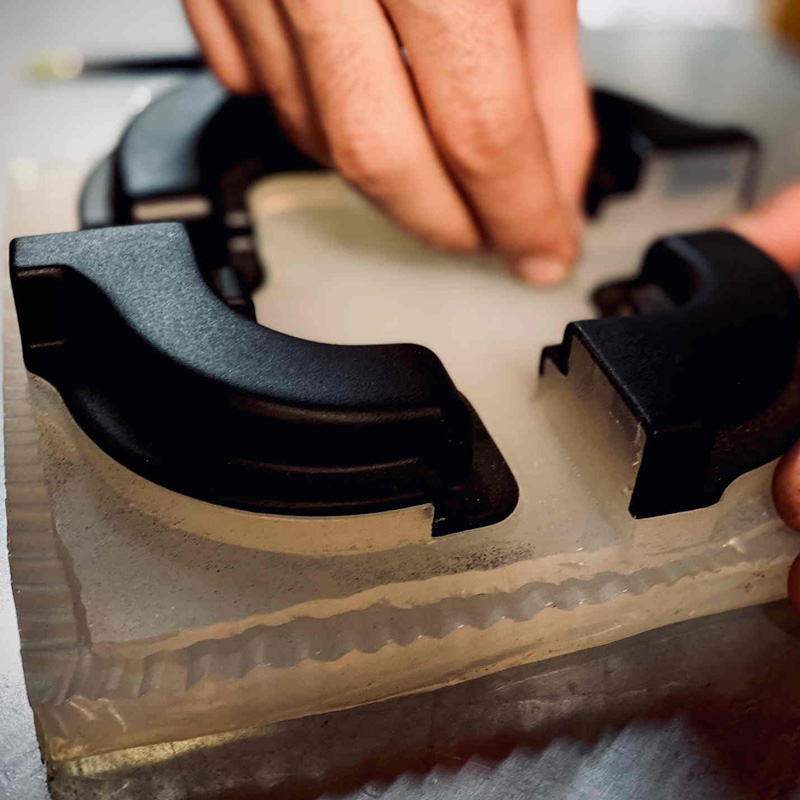
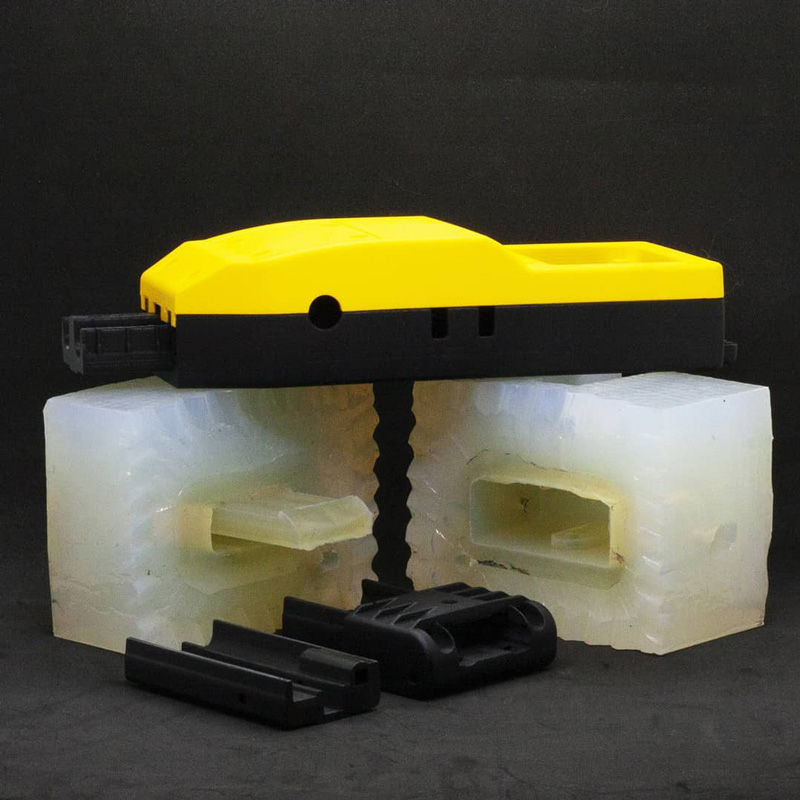
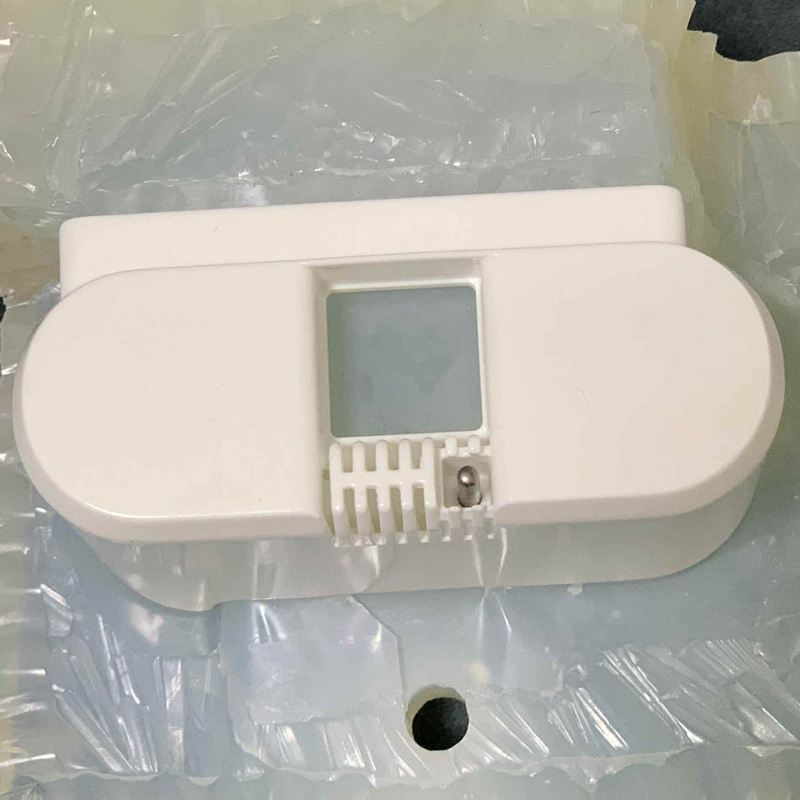